 |
|
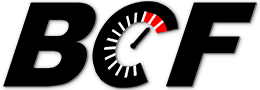 |

|
Author |
Message |
Nope. |
This post is not being displayed .
|
 Nope. World Chat Champion
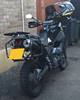
Joined: 17 Feb 2011 Karma :   
|
 Posted: 16:26 - 02 Aug 2023 Post subject: Milling Machine Project - Gate 301 |
 |
|
For many years now I've lusted after a milling machine of my own, but a combination of space, power, and ease of movement issues compounded into it not happening. That is, until the 6th of July this year when I spotted an advert for a Gate Turret Mill on Facebook Marketplace for just £400. The advert stated that it was located just down the road from me in Berkhampsted, and not much else. These are the advert photos:
https://live.staticflickr.com/65535/53076787266_daeb2c2ec7.jpg
https://live.staticflickr.com/65535/53076214227_4a3d6e605d.jpg
https://live.staticflickr.com/65535/53076787236_03e26d156f.jpg
https://live.staticflickr.com/65535/53077288908_04ee8084df.jpg
https://live.staticflickr.com/65535/53076214207_ca47981074.jpg
https://live.staticflickr.com/65535/53076983734_bd8799f172.jpg
I promptly messaged the chap, and over the course of about a week managed to ascertain that it was actually located in Kent. He said that he had a forklift that could lift it to load, and was happy to arrange collection. He had some personal stuff going on so I wasn't actually able to arrange collection until the end of July, but once I had, a good friend of mine kindly agreed to give me a hand shifting it.
On a Thursday evening we hooked up the trailer and set off for Kent. Once we had arrived at the chaps unit the full scale of this milling machine became clear - it's a beast! Exactly what I wanted though, which is great. The machine was helpfully already on a pallet, so in theory it should've just been a case of hoiking it up with the fork lift and dropping it on the trailer, but of course these things are never that simple! Firstly there was supposed to be a large forklift available, but since the chaps last visit to his yard this one seems to have gone missing and all that could be found was a tiny forklift with a maximum lifting capacity of 1.1 tonnes, and with no operable brakes. This presented an issue as this milling machine weighs about 1.7 tonnes! We tried to lift it, but of course after much hydraulic groaning not a lot happened:
https://live.staticflickr.com/65535/53076787591_e93bc54801.jpg
So, in lieu of any other ideas, we decided to split the machine at the swivel. Luckily the forklift was capable of doing this:
https://live.staticflickr.com/65535/53077289218_06267f0abe.jpg
Doing this we managed to get the ram & head onto one side of the trailer, and the base unit onto the other side. We got this strapped down and headed off on the long journey back to Creslow. We pulled in to check the straps after a short while just to make sure:
https://live.staticflickr.com/65535/53076983989_4f63a0fbdd.jpg
But happily nothing had moved. We arrived back to the yard about 2am, I wrapped the machine up in plastic, and we went home to sleep intending to unload it the next day.
Arriving the next day I found that everything was nice and dry which was great, and we set about unloading stuff from the trailer. The forklift at the yard is much better than the one we used to collect the machine, but it still has it's issues so we had fun and games unloading again! Happily my friend is a much more experienced forklift pilot than I am so agreed to assist:
https://live.staticflickr.com/65535/53089125423_ff2401b3d5.jpg
https://live.staticflickr.com/65535/53089125348_dfb6af96ca.jpg
https://live.staticflickr.com/65535/53088818239_780809b95d.jpg
https://live.staticflickr.com/65535/53088636556_95e24dba5f.jpg
https://live.staticflickr.com/65535/53088636976_9a8cf76d92.jpg
https://live.staticflickr.com/65535/53088636836_263fd088dc.jpg
Unfortunately the fork lift is slightly too high to fit into the garage, so once it was at the door we were on our own! We tried initially placing the machine on a trolley we found, but this didn't look like it was up to the task so we resorted to rolling it in on scaffolding poles:
https://live.staticflickr.com/65535/53089127438_b3eb23bb1c.jpg
The ram then went on another little trolley for ease of movement:
https://live.staticflickr.com/65535/53089038640_6e065446e7.jpg
I'd balanced it on some old wood for east of dropping it off of the fork lift onto the pallet, but this proved fairly unstable so I sought to adjust this through the strategic placement of some hydraulic jacks:
https://live.staticflickr.com/65535/53088821769_e1c5df6e47.jpg
https://live.staticflickr.com/65535/53088638636_ca06e49b68.jpg
This was, in hindsight, not the safest thing to do, but it did get the job done. Now, when we'd been loading the machine it had become clear that the rams adjustable position from the swivel boss was completely seized. I tried moving the handle etc. but to no avail, so I soaked the thing in a whole can of penetrating oil and left it over night. That evening I took a trip to pick up a used pump truck for £60:
https://live.staticflickr.com/65535/53089041505_9b34a7e531.jpg
Which I promptly took up the yard the next day. Having this pump truck meant that the sketchy plastic trolly that the ram was on could be retired, but first I had to get the pallet off of it. Back to the fork lift!
https://live.staticflickr.com/65535/53089130148_88329cea46.jpg
And it's off:
https://live.staticflickr.com/65535/53088072897_3c3ca1121d.jpg
I then turned by attention to the rest of the mill, and found that the suds tray was still full of manky old suds:
https://live.staticflickr.com/65535/53089041120_35a8269b82.jpg
This was promptly sucked out with my fathers workshop Vax in liquid mode:
https://live.staticflickr.com/65535/53088643796_1fcc71cb54.jpg
I then turned my attention back to the seized ram. With the ram lifted off of the pallet and the swivel boss in the air I figured I had the best change of freeing it off with the least weight on it. Posting on [url=https://www.reddit.com/r/Machinists/]r/machinists someone suggested that it might be possible that the ram is pinned in place to avoid factory machinists adjusting it. I checked everywhere and found nothing like this. I removed all of the gib bolts and loosened all of the adjusters. The shaft would move slightly and tension the adjustment chain, but the boss wouldn't move.
https://live.staticflickr.com/65535/53088827664_fe7ef4fb98.jpg
I strapped the ram to the pallet such that it couldn't move and my father and I attempted to use a piece of wood and a sledge hammer to free it off. Still not movement, still no joy. About this time a friend arrived and I went to give him a tour of the site. In the mean time my father carried on with the wood and sledge hammer method, and by the time we'd gotten back he had managed to free it off!
https://live.staticflickr.com/65535/53088645991_bcaec146d9.jpg
This was great news as freeing this off was looking like it was going to be a nightmare, but it now moves with relative ease and I'm certain once I've got some slideway oil on there it'll be right as rain.
I then set about cleaning the pretty disgusting motor fan on the spindle drive motor:
https://live.staticflickr.com/65535/53088644661_476acd438f.jpg
https://live.staticflickr.com/65535/53089045860_735738c5e9.jpg
https://live.staticflickr.com/65535/53089135798_f99ab9ce54.jpg
It's clear that this needs some more cleaning but it's still quite a bit better than before.
Next up I decided to power up the core of the machine to test the various systems. Obviously the main spindle motor isn't currently attached (it also has a broken terminal box - more on that later) but the rest of the systems such as the power feed and the suds pump are connected.
https://live.staticflickr.com/65535/53088078432_8335aa59e9.jpg
https://live.staticflickr.com/65535/53088078727_197aeaf8a3.jpg
https://live.staticflickr.com/65535/53089137623_428c9b1e79.jpg
Sure enough the suds pump worked fine, but the power feed motor span a bit and then stopped. I decided to remove the back of the motor to take a look, and as soon as I did liquid oil started pouring out:
https://live.staticflickr.com/65535/53088830019_916316b506.jpg
https://live.staticflickr.com/65535/53089138738_dd55f0074c.jpg
Which isn't really what I expected from an electric motor without sealed end caps. My theory is that this is decomposed grease and the motor needs the bearings re-packing.
The motor being apart revealed nothing obvious other than some very light corrosion on the commutator, so I re-assembled it and tried again. This time the motor span a bit but then stopped again. It then became clear that the issue was likely inside the powerfeed gearbox. I drained the gearbox oil and popped the side casing off:
https://live.staticflickr.com/65535/53088648261_8f164a841f.jpg
https://live.staticflickr.com/65535/53088079897_7fe8bae95d.jpg
It looks fairly clear from inside the box that there is a wheel on the motor shaft that is both in the wrong place and extremely worn. It is not immediately clear to me what this wheel is for nor what it should look like. I currently don't have a parts diagram or manual for this machine so I think in order to fix this I'm going to need those. It seems the only online resource for these charges £95 for them which isn't ideal, but it's currently looking like the only option.
We packed up and went home for the day at this point, intending to come back the next day. Unfortunately on Sunday morning my father had to be rushed to hospital so obviously we were unable to make any real further progress on the machine. I did pop up for 20 minutes to take some measurements of a couple of bits. Firstly this switch:
https://live.staticflickr.com/65535/53089140863_8db7ae5cc3.jpg
and secondly the broken motor fan from the power feed:
https://live.staticflickr.com/65535/53089051790_6edebca82b.jpg
I took these measurements home and drew up replacement parts in Fusion 360:
https://live.staticflickr.com/65535/53088812849_d0910814d5.jpg
https://live.staticflickr.com/65535/53089119823_0a2972d760.jpg
https://live.staticflickr.com/65535/53088061747_9a756db4c2.jpg
https://live.staticflickr.com/65535/53089119653_8d7a2efef4.jpg
I then setup the 3D printer (Creality Ender 5 Plus), sliced the models, and set them to print:
https://live.staticflickr.com/65535/53088834619_2c0fc9fcc1.jpg
https://live.staticflickr.com/65535/53089119713_03d9843533.jpg
https://live.staticflickr.com/65535/53088812734_ab47ff636d.jpg
https://live.staticflickr.com/65535/53089119778_f428f246e7.jpg
https://live.staticflickr.com/65535/53089142708_0f0c733516.jpg
https://live.staticflickr.com/65535/53088631371_051e3a7ed4.jpg
https://live.staticflickr.com/65535/53088814384_cdf18a57f1.jpg
https://live.staticflickr.com/65535/53088814379_3400739295.jpg
The prints need a little cleaning up but nothing crazy. I noted when I was making a model of the motor fan that the blades were straight and found this odd, but having printed it I now note that it moves very little air. It's possible that the motor cowling assists in this, but ultimately I think I'll probably re-design it again to have curved blades to actually move air over the motor housing.
That's all for now. I'm unlikely to make much further progress until my father is more stable as I'm visiting him in hospital most evenings at the moment, but I'm hoping fairly soon I can re-wire the spindle motor, test that, fix the gearbox, put the ram back on the mill and get it into place! ____________________ 2011 XT660Z Ténéré - 2003 YZR-R1 5PW (In Build) |
|
Back to top |
|
You must be logged in to rate posts |
|
 |
Pete. |
This post is not being displayed .
|
 Pete. Super Spammer

Joined: 22 Aug 2006 Karma :     
|
 Posted: 17:40 - 02 Aug 2023 Post subject: |
 |
|
That's a damn nice machine and a bloody good bargain. The rotary table is worth at least half what you paid. Is the taper 30 or 40 size? 40 is stronger and more plentiful. Nice that you got the ISO-morse taper adapter.
If it's the worm on the gearbox that's worn then so long as it's engaging then it should do. If you need a gear cut let me know.
The motor fan is supposed to have straight blades because it has to work in both directions. It won't work without the end bell attached because it's a centrifugal fan not an axial one. What you have printed there is perfect.
BTW I have a bunch of those ceramic fuse holders if you find you need spares. ____________________ a.k.a 'Geri'
132.9mph off and walked away. Gear is good, gear is good, gear is very very good  |
|
Back to top |
|
You must be logged in to rate posts |
|
 |
Nope. |
This post is not being displayed .
|
 Nope. World Chat Champion
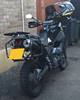
Joined: 17 Feb 2011 Karma :   
|
|
Back to top |
|
You must be logged in to rate posts |
|
 |
Pete. |
This post is not being displayed .
|
 Pete. Super Spammer

Joined: 22 Aug 2006 Karma :     
|
 Posted: 17:21 - 03 Aug 2023 Post subject: |
 |
|
The loose thin wheel appears to be the end plate that should be keeping the oil in the gearbox. It'll be the reason you got oil out of the motor, should be filling that hole you can see. ____________________ a.k.a 'Geri'
132.9mph off and walked away. Gear is good, gear is good, gear is very very good  |
|
Back to top |
|
You must be logged in to rate posts |
|
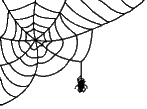 |
Old Thread Alert!
There is a gap of 240 days between these two posts... |
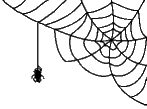 |
|
Nope. |
This post is not being displayed .
|
 Nope. World Chat Champion
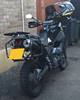
Joined: 17 Feb 2011 Karma :   
|
 Posted: 20:46 - 30 Mar 2024 Post subject: |
 |
|
So, as I mentioned in my previous post, the power feed gearbox on the table had a loose ring inside it and it wasn't immediately obvious which end of the input shaft this was supposed to be on. Further, the ring had become damaged after multiple impacts with one of the gears and thus needed to be replaced anyway.
I have a manual for the machine now, but it leaves a lot to be desired and it's mention of the gearbox is confined to a small section about installation and one diagram which is frankly worse than useless. Regardless, I needed to remove the motor to remove the input shaft, and so I set about figuring out how to do that. Firstly, there are no bolts going from the motor housing into the gearbox housing, and no bolts going from the gearbox housing into the motor housing. All there is is just this one bolt under the gearbox outer cover which points in the direction of the motor:
https://live.staticflickr.com/65535/53099390207_2b43214b82.jpg
I also removed the top cover to check there was nothing there and gave it a little clean whilst I was there:
https://live.staticflickr.com/65535/53099390657_8dc5a62b0a.jpg
https://live.staticflickr.com/65535/53100452823_f91fb3a0a5.jpg
So, with that bolt under the cover being the only obvious retention method, I set about trying to remove it. It became obvious at this point that somebody previously has been here as the bolt head was completely rounded off! I tried hammering a Torx bit into it but that just turned as well, and a stud extractor did much the same. It was at this point I resigned myself to drilling it out, and spent the next 45 minutes or so working on drilling it out. Even when I'd measured and double measured the distance I'd drilled, the motor housing would still not move. I could rock it back and forth rotationally, but as for movement outwards there was nothing.
After a couple of hours of this and multiple opinions from other people, we decided to just try and whack it out, come what may. There was no obvious other fixing, there was no other retention, and it had to come out. I used an old jack handle as a drift and hammered it, but it still didn't really want to move. We applied some leverage and unfortunately the casting gave way:
https://live.staticflickr.com/65535/53099949506_e81d522215.jpg
https://live.staticflickr.com/65535/53100138164_cb353e1afc.jpg
Bugger.
At least the shaft moves back and forth now. At this point I realised that the wheel was jammed against the gear again, and the shaft wouldn't move back with the wheel in place. If I had been thinking straight at this point I probably would've stopped and re-assessed the whole situation, but just wanting the damn thing out I took a dremel to the edge of the wheel to make it clear the gear. This isn't terrible as it was already damaged and I need to make a new one anyway.
https://live.staticflickr.com/65535/53100452233_dd983c34c3.jpg
https://live.staticflickr.com/65535/53100359250_fffd5847b3.jpg
Of course, at this point the other half of the casting is still stuck in the gearbox. Being able to look at it head on meant that it became clear that the top retaining bolt that I had drilled out was actually partially still holding the ring in place as it was at an angle and the drill bit hadn't quite managed to take the furthest edge. I tried to drill out the rest, however at this point the drill bit snapped in the hole. This necessitated drilling out a piece of the aluminium mounting casting to get purchase and extract the drill bit, which happily came out without too much hassle.
I managed with some brute force and ignorance to hammer out the rest of the mounting ring, and with it the shaft came free.
https://live.staticflickr.com/65535/53100142019_cc781513ae.jpg
https://live.staticflickr.com/65535/53100357485_560b81af6c.jpg
https://live.staticflickr.com/65535/53100136659_b02fd8e44c.jpg
With it out, it became clear that there was in fact a second fixing method. The bottom of the ring is held in place by another bolt, but where could this be accessed from?
https://live.staticflickr.com/65535/53099947331_1ff978d92e.jpg
Well, it turns out that behind one of the case cover mounting bolts is another bolt. Again, with a tiny allen key head that had been partially rounded off.
https://live.staticflickr.com/65535/53100444928_2e5a5d1707.jpg
It also didn't help that whomever had re-fitted the gearbox cover plate last time had used silicon sealant and had put enough on that it had gone down the bolt hole and made it impossible to access the head. Once this was extracted I could focus on getting the bolt out:
https://live.staticflickr.com/65535/53099382532_a17a1b42bf.jpg
This time the stud extractor worked, but that bolt is damaged and the last person that was here really knackered the head.
So, now with a broken casting and the retaining fixtures out of the way, I headed home to figure out how to make a new one. I initially considered just having a friend TIG weld it back together so I could true it up on the lathe and re-use it, but the damage to it is fairly significant and not being an incredibly complex part this seemed like a short cut way of doing it. I then thought I'd turn a new one up out of 6" bar stock, but I don't have any and it seems the prices have shot through the roof, so I didn't fancy machining 80% of a bar away at £70 a go.
Regardless, I drew it up in CAD and 3d printed a prototype:
https://live.staticflickr.com/65535/53099383137_c195331988.jpg
I took this up the next day and sure enough it fit so I know the drawing is good. This got me thinking about how to better retain the motor as even though I will helicoil the hole I drilled out, and I will also fit a longer lower casing bolt to utilise the bottom retainer, I don't like this method and think it leaves margin for error. In order to necessitate better access to the gearbox I decided to remove it from the machine, something I wish I had done the day prior:
https://live.staticflickr.com/65535/53100353500_793f7b4614.jpg
https://live.staticflickr.com/65535/53099381937_c5dbb4e902.jpg
https://live.staticflickr.com/65535/53099942521_487a674949.jpg
https://live.staticflickr.com/65535/53100470273_0ffc8bdc05.jpg
Luckily it came off without too much of a fight:
https://live.staticflickr.com/65535/53100158559_706526823d.jpg
https://live.staticflickr.com/65535/53100378330_568c932f7e.jpg
https://live.staticflickr.com/65535/53100378000_87a1794ce8.jpg
I then noticed that the motor end housing that had come off the day prior with half of the casting also hadn't survived the removal session unscathed, as it is ever so slightly bent with a tiny crack on one side:
https://live.staticflickr.com/65535/53099405872_0dbcc186c0.jpg
https://live.staticflickr.com/65535/53099405267_e2a01950d5.jpg
Really not ideal, and a lesson in why to sit back and properly consider things in future.
So, there are several things that I now need to do:
- Re-design the motor mount to better hold the motor
- Make a new motor mount
- Helicoil the drilled out gearbox hole
- Repair or replace the motor end housing (or the whole motor if it comes to it)
Sigh.
So, I gave it some thought and decided that the best course of action was to improve the mount by adding bolts from the outside that directly connect it to the gearbox. For this, I'm going to need to drill and tap two holes in the gearbox casing but I think this should be fairly simple (hopefully!). I measured up the supporting ribbing inside the gearbox and made notes of where it is so my holes could avoid it. I then went home and drew up & prototyped some parts:
https://live.staticflickr.com/65535/53099967166_6c03510881.jpg
https://live.staticflickr.com/65535/53100466973_129d8b04d3.jpg
https://live.staticflickr.com/65535/53099965721_270081d01e.jpg
https://live.staticflickr.com/65535/53100375265_d75783d28f.jpg
https://live.staticflickr.com/65535/53100154949_b5e9ba8e40.jpg
The way this works is the extended circle around the mount offers an addition edge on which to mount a bolting block that can then be attached by threaded bolts to the ring & to the gearbox housing.
https://live.staticflickr.com/65535/53100327739_ae516f3f14.jpg
https://live.staticflickr.com/65535/53099575252_8f6ca228e9.jpg ____________________ 2011 XT660Z Ténéré - 2003 YZR-R1 5PW (In Build) |
|
Back to top |
|
You must be logged in to rate posts |
|
 |
Nope. |
This post is not being displayed .
|
 Nope. World Chat Champion
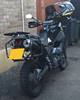
Joined: 17 Feb 2011 Karma :   
|
 Posted: 20:48 - 30 Mar 2024 Post subject: |
 |
|
So, for the past few months this milling machine has been in two sections on two pallets taking up a large amount of space in my workshop. This hasn't been an issue as I really haven't had the time to get up there and do anything, but having had some time this weekend just gone I thought I might as well start looking at sorting it out!
https://live.staticflickr.com/65535/53089038640_6e065446e7_c.jpg
The first thing we did was drag the ram and head arrangement out of the garage using the pump truck, and free up the slideway that allows the head to be moved backwards and forwards. Once it was freed up again I greased it up and worked it back and forwards so it hopefully won't seize again any time soon.
https://live.staticflickr.com/65535/53610829169_8825ca03a1_c.jpg
Then I dragged the main body of the milling machine outside.
https://live.staticflickr.com/65535/53610706478_a580429fff_c.jpg
I then fired up the forklift, strapped the light end of the ram to one of the forks (it's very front heavy!), and picked it up off of the pallet.
https://live.staticflickr.com/65535/53610706018_a30742460a_c.jpg
With a bit of finagling we manoeuvred the body of the mill underneath the ram, and lined everything up.
https://live.staticflickr.com/65535/53610943610_5b06b06768_c.jpg
Dropped it down until the bolts were almost engaged, and then used the pump truck to lift it up the last few mm to engage everything before dropping the ram down and tightening up the bolts.
https://live.staticflickr.com/65535/53610705058_aeb80f04fb_c.jpg
https://live.staticflickr.com/65535/53610943325_6da55b88b7_c.jpg
In order to fit it in under the door I had to pivot the head over 90 degrees (almost).
https://live.staticflickr.com/65535/53610489566_3eaa3d2fa0_c.jpg
We then, enlisting the help of another friend, dragged it inside on the pump truck and moved it roughly into position. We now had the problem of how to get the (collapsing!) pallet out from underneath it. Numerous options were thrown around, but in the end we decided to go with the easiest (and probably most sketchy) way. First, we lifted the machine up on the pump truck and put two blocks of wood under the front:
https://live.staticflickr.com/65535/53610943105_3acfd24598_c.jpg
We then put a block of wood under the back of the ram on a trolley jack, dropped the pump truck, and removed the pallet!
https://live.staticflickr.com/65535/53610489586_99f8690404_c.jpg
We then dropped the back down as low as we could, smacked the blocks out, and she was in place!
https://live.staticflickr.com/65535/53609616497_74022cb405_c.jpg
That took just about all day. Next time hopefully I'll be casting the final motor mount, affixing it to the gearbox, getting the motor running, and getting the whole machine up and going! ____________________ 2011 XT660Z Ténéré - 2003 YZR-R1 5PW (In Build) |
|
Back to top |
|
You must be logged in to rate posts |
|
 |
Nope. |
This post is not being displayed .
|
 Nope. World Chat Champion
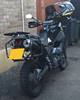
Joined: 17 Feb 2011 Karma :   
|
 Posted: 20:54 - 30 Mar 2024 Post subject: |
 |
|
So, with the milling machine in place in the workshop, it was time to turn my attention back to the power feed gearbox motor mount that I unceremoniously broke back in October. I had designed a replacement with a new mount system and 3D printed a prototype back then, but now it was time to actually make one. Onwards!
So, with the requirement to make a new motor mount for the power slide and the pretty high cost of aluminium bar stock these days, I decided it was of course sensible to dive deep into a new rabbit hole of metal casting!
I've wanted to cast my own parts for a while now, but never had a good enough excuse to make the investment of time & money in my own mini-foundry, then this came along and it seemed like the perfect excuse!
First things first, I went on eBay and ordered a Vevor 12kg Propane Melting Furnace kit which comes with a 12kg graphite crucible, stainless steel furnace shell, ceramic insulating material, a bag of refractory cement, some tongs, and dual propane burners. This isn't the be all and end all of furnaces by any means, but it's a great starting place and I only paid £124 for the kit including shipping. I then went and bought some proper crucible tongs as the ones included don't look fantastic. I got a set of lifting tongs and a set of pouring tongs on eBay as well, and they cost £60.
With tooling out of the way, I had to look to the consumable areas of smelting. Firstly, I needed sand. Not just any sand will do, and there are various types of sand which can be used for casting. "Green sand" is what is traditionally used, and this is made of a mixture of sand, clay, and water. Depending upon what grade of sand you use depends on what quality of surface finish you get. You can also go down a more professional route and use an oil based sand such as Bentomix, but this is very expensive (comparably) and only something I think I'll look at once I've got the full hang of all of this. I ended up ordering 20kg of Bromsgrove Greensand from [Artisan Foundry Store](https://www.artisanfoundry.co.uk/product_info.php?products_id=38).
The next thing I needed was a parting agent. A lot of backyard foundries seem to use talc, but apparently this can cause a poor surface on the casting. I did some research and settled on Calcium Carbonate as apparently this is an excellent release agent and doesn't affect the surface of the casting. Originally I was only going to order 1 - 5kg's of the stuff, but it turns out that 5kg is as expensive as 25kg! So of course I ordered 25kg off of eBay. I also needed a special thin mesh bag to sprinkle it with, which I also ordered off of Artisan Foundry Store.
With all of that ordered, there were three more things I needed to do before I could get going:
1. Make the parts from which to make the casting
2. Make the moulding flask
3. Buy propane
I decided to start out by modifying the models for casting. The original drawings were to use as prototypes, but in order to cast these ready for machining I needed to make some modifications.
First, I removed all of the holes & centre bore, and added some 4.2mm holes in which I could embed brass threaded collars:
https://live.staticflickr.com/65535/53104540954_9101851c8a_c.jpg
https://live.staticflickr.com/65535/53104838488_a0c9e80448_c.jpg
https://live.staticflickr.com/65535/53104540959_535923f2f5_c.jpg
https://live.staticflickr.com/65535/53104541094_bb8cc8de3f_c.jpg
I additionally enlarged the parts by 2-3mm on all planes such that there was space to machine the surfaces on the lathe. Then I printed them:
https://live.staticflickr.com/65535/53104542524_3785b718f7_c.jpg
Once they were done printing 14 hours later, I embedded the small brass threaded collars using a soldering iron:
https://live.staticflickr.com/65535/53104839728_78bb60ee9a_c.jpg
Then I screwed in the brass studs temporarily:
https://live.staticflickr.com/65535/53104542109_b40c137fbf_c.jpg
The brass holes/studs are there such that when the item is packed in sand it can have the studs screwed in and be pulled up, hopefully without disturbing the sand surface.
I then put it in the casting drag, and then applied a layer of calcium carbonate parting powder:
https://live.staticflickr.com/65535/53617814454_1d18d55752_c.jpg
I then packed in some green sand:
https://live.staticflickr.com/65535/53617931100_dc313d6f6f_c.jpg
I also obviously made the cope to match the drag with the sprue and vent hole but I of course forgot to photograph this.
I then cut up some scrap aluminium wall decorations and started the little Vevor furnace:
https://live.staticflickr.com/65535/53617486111_fbeb1aaa73_c.jpg
https://live.staticflickr.com/65535/53617927630_cf3c32a017_c.jpg
I kept feeding aluminium scrap in until I felt I had enough molten aluminium to make the pour:
https://live.staticflickr.com/65535/53617818624_a8e391f640_c.jpg
Then I lifted out the crucible, scraped off the slag, and made the pour (along with some ingots for the extra):
https://live.staticflickr.com/65535/53617816384_e88b227398_c.jpg
Once it'd cooled down a bit I knocked out the sand and removed the casting!
https://live.staticflickr.com/65535/53617481641_f856689667_c.jpg
It wasn't the cleanest casting, but it also wasn't the worst. There was some areas where sand had fallen in and this caused some surface defects, plus a couple of deep ones, but the majority of these would be machined out and the ones that wouldn't were non-structural, so good enough for me!
I then chopped off the sprue, runner, and vent:
https://live.staticflickr.com/65535/53617486896_39012c0cb8_c.jpg
Popped it into the 4 jaw chuck on the little Myford ML7 and set about machining it. This alloy was quite difficult to machine well, it really didn't want to play nice and no matter what speeds & feeds I used it, frankly, machined like crap with varying levels of hardness throughout. I guess that's what you get for using a mix of scrap, along with some pretty old and well used tool tips.
https://live.staticflickr.com/65535/53617926715_2fc17da6c0_c.jpg
https://live.staticflickr.com/65535/53616610957_f0aa972985_c.jpg
https://live.staticflickr.com/65535/53617483616_9bc5e195dd_c.jpg
https://live.staticflickr.com/65535/53617691398_2833db52a4_c.jpg
https://live.staticflickr.com/65535/53617814199_5704645902_c.jpg
https://live.staticflickr.com/65535/53617486356_51171255a2_c.jpg
https://live.staticflickr.com/65535/53617816764_c4505b0f1d_c.jpg
Testing it with the motor nose casing:
https://live.staticflickr.com/65535/53616605262_d255e6003f_c.jpg
I fitted the shaft seal, but you can see some of the mild porosity/sand ingress in the casting in this photo. Still, it'll do the job and I can't be bothered to do it again for something nobody will ever see:
https://live.staticflickr.com/65535/53621017661_2de86b1d8f_c.jpg
The motor nose casing was slightly bent so I re-shaped it, replaced the shaft seal, and bolted up the commutator:
https://live.staticflickr.com/65535/53621226193_fc0f5b4417_c.jpg
https://live.staticflickr.com/65535/53621465205_2d227f1912_c.jpg
I re-assembled the motor, but when power was applied from the mill controls the motor just vibrated and made a noise like an angry swarm of wasps in harmony. I figured there were two key possibilities: 1) The windings were shorted, or 2) A phase wasn't working. I pulled the commutator out again and thoroughly cleaned the inside of the motor out with brake cleaner to remove any trace of the oil that had been in there that had previously leaked through from the gearbox. I then checked the windings with a multimeter and found them all to be in good order:
https://live.staticflickr.com/65535/53621465095_99da109afa_c.jpg
This suggested the issue was likely a phase not working, so I checked the fuses, and this one was blown:
https://live.staticflickr.com/65535/53620142827_a34d6ea23d_c.jpg
I swapped one of the other ones in to test, and the motor (noisily!) span up! So that's one problem down.
Now I know that the motor is good, I can drill the mount for the motor mounting holes. I didn't want to do this if I was going to have to replace the motor, so now I know it works I can crack on!
I marked up the mount and used the pillar drill to drill the holes and the counter sinks for the bolt heads (this photo is the first two of the four):
https://live.staticflickr.com/65535/53621464990_040be87b50_c.jpg
and the motor nose bolted up perfectly:
https://live.staticflickr.com/65535/53621464970_5f6e4b4967_c.jpg
and it fits up to the gearbox nicely!
https://live.staticflickr.com/65535/53621350679_634dc90af7_c.jpg
https://live.staticflickr.com/65535/53621017161_d63ce7c4c7_c.jpg
I was then planning to drill the gearbox casing, tap it, and bolt the mount up using the extended ring, however I discovered the tap I thought I had for the bolts was the wrong thread pitch. I have however now borrowed one from my neighbour, so hopefully I can get this finished tomorrow (Easter Sunday)! I realised that my original idea of the extension piece might interfere with the motor nose, so I'm holding off on that one in the hope that this will be enough retention for the motor. ____________________ 2011 XT660Z Ténéré - 2003 YZR-R1 5PW (In Build) |
|
Back to top |
|
You must be logged in to rate posts |
|
 |
Nope. |
This post is not being displayed .
|
 Nope. World Chat Champion
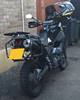
Joined: 17 Feb 2011 Karma :   
|
 Posted: 23:43 - 01 Apr 2024 Post subject: |
 |
|
So, with my neighbours tap in hand and a borrowed tap kit from my father (which also included an M6x1.00 tap), we (my father and I) set off back to the workshop.
Problem one was that the gearbox has handles on the opposing face to the motor mount, so it won't lie flat on its front, and regardless of that, the box itself wouldn't fit within the travel of my little pillar drill. I obviously needed the holes to be cut straight, so I made up a quick drilling block on the pillar drill and used that for the guide. I first used a 3mm drill bit, marking and drilling the new mounting ring first, and then marking the gearbox through the hole. I used a punch to create an indentation to locate the drill bit in, and then aligned the quickly made drill block:
https://live.staticflickr.com/65535/53626374249_2e3494c53a.jpg
I drilled it out 3mm first, and then 5mm as required for an M6 tap. I then tapped the hole:
https://live.staticflickr.com/65535/53626374244_5190926838.jpg
and test fitted with the motor nose attached to the mount:
https://live.staticflickr.com/65535/53625149202_ee1ed6e8fc.jpg
I then repeated the process with hole 2:
https://live.staticflickr.com/65535/53626243088_caf639808c.jpg
all looking good so far:
https://live.staticflickr.com/65535/53626047921_3017636c4e.jpg
and finally hole 3 (showing the drill block I made for the 5mm drill bit):
https://live.staticflickr.com/65535/53626243053_11f416caf1.jpg
and it all fits up nicely!
https://live.staticflickr.com/65535/53626487665_0d6bcefe29.jpg
https://live.staticflickr.com/65535/53626243043_4343a6a273.jpg
So I re-assembled the motor and fixed on the mount:
https://live.staticflickr.com/65535/53625149122_21a4fa7aa6.jpg
https://live.staticflickr.com/65535/53626243008_3527752572.jpg
re-attached the gearbox to the mill:
https://live.staticflickr.com/65535/53626487625_f99f0176c9.jpg
re-installed the motor drive shaft along with the circlips for the bearing and the shaft end:
https://live.staticflickr.com/65535/53626242988_8a16d3ce2f.jpg
https://live.staticflickr.com/65535/53626374169_c2f12c61ca.jpg
I also re-packed the front bearing and re-installed the cover plate. I then put gasket sealant on the mating face of the mount and the nose engagement piece to create an oil seal, fitted the woodruff key into the shaft, and installed the motor!
https://live.staticflickr.com/65535/53626242978_b1d2d4b24e.jpg
https://live.staticflickr.com/65535/53626487585_ab6a935ab5.jpg
https://live.staticflickr.com/65535/53626242928_352028cfee.jpg
I then added gasket sealant to the surface of the gearbox cover plate and affixed that:
https://live.staticflickr.com/65535/53626487535_7d4926a9d1.jpg
and with a quick test, it worked!
https://www.youtube.com/shorts/duEGrliDqWY
I then left the RTV overnight to dry before going back today and adding gearbox oil to it. I need to find something to replace the missing oil wicks, I think probably cotton pipe cleaners will work, but I'll test their wicking qualities this week and see.
Then, finally, I burned the old workshop cabinets in the firepit:
https://live.staticflickr.com/65535/53626374044_ace47c19ff.jpg
https://live.staticflickr.com/65535/53626374059_a7e46aa320.jpg
https://live.staticflickr.com/65535/53626374034_1ac408b59c.jpg
https://live.staticflickr.com/65535/53626487630_90f968dc87.jpg
All in all a very successful and decent Easter Bank Holiday! Next step is to replace the connection block on the main top motor & replace the cover, and possibly look at replacing the damaged belt cover, though that's just cosmetic. Not long until I have a fully working machine I think! ____________________ 2011 XT660Z Ténéré - 2003 YZR-R1 5PW (In Build) |
|
Back to top |
|
You must be logged in to rate posts |
|
 |
stinkwheel |
This post is not being displayed .
|
 stinkwheel Bovine Proctologist
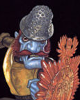
Joined: 12 Jul 2004 Karma :    
|
 Posted: 00:03 - 02 Apr 2024 Post subject: |
 |
|
Given the amount of machining you landed up having to do anyway, you have to wonder if it would have been better to just cast more of a blank and machine it down afterwards. Then at least any inclusions would have been in the bit you were turning off and there are less fiddly bits to cool unevenly.
In my admittedly very limited experience of green sand casting, it seems that the sand gets better at taking and keeping the form after it's been used a few times. Maybe the heat does something to the silica grain structure? Yours looks a little on the damp side too. ____________________ “Rule one: Always stick around for one more drink. That's when things happen. That's when you find out everything you want to know.”
I did the 2010 Round Britain Rally on my 350 Bullet. 89 landmarks, 3 months, 9,500 miles. |
|
Back to top |
|
You must be logged in to rate posts |
|
 |
Nope. |
This post is not being displayed .
|
 Nope. World Chat Champion
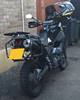
Joined: 17 Feb 2011 Karma :   
|
|
Back to top |
|
You must be logged in to rate posts |
|
 |
stinkwheel |
This post is not being displayed .
|
 stinkwheel Bovine Proctologist
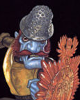
Joined: 12 Jul 2004 Karma :    
|
|
Back to top |
|
You must be logged in to rate posts |
|
 |
Pete. |
This post is not being displayed .
|
 Pete. Super Spammer

Joined: 22 Aug 2006 Karma :     
|
 Posted: 06:45 - 02 Apr 2024 Post subject: |
 |
|
Heroic
As you've found, fresh-cast ally is a gummy mess to machine. If you have to do it again find an old ally wheel to smash up they have high silicon content. Used to be the best ally for home casting was old hard drive casings but of course they are not so commonly found now and very much smaller when you do. ____________________ a.k.a 'Geri'
132.9mph off and walked away. Gear is good, gear is good, gear is very very good  |
|
Back to top |
|
You must be logged in to rate posts |
|
 |
stinkwheel |
This post is not being displayed .
|
 stinkwheel Bovine Proctologist
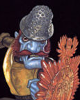
Joined: 12 Jul 2004 Karma :    
|
|
Back to top |
|
You must be logged in to rate posts |
|
 |
Freddyfruitba... |
This post is not being displayed .
|
 Freddyfruitba... World Chat Champion
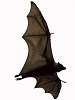
Joined: 20 May 2016 Karma :   
|
|
Back to top |
|
You must be logged in to rate posts |
|
 |
Nope. |
This post is not being displayed .
|
 Nope. World Chat Champion
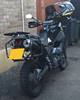
Joined: 17 Feb 2011 Karma :   
|
 Posted: 13:48 - 05 Apr 2024 Post subject: |
 |
|
Pete. wrote: | Heroic
As you've found, fresh-cast ally is a gummy mess to machine. If you have to do it again find an old ally wheel to smash up they have high silicon content. Used to be the best ally for home casting was old hard drive casings but of course they are not so commonly found now and very much smaller when you do. |
Thanks! Happily I've got an old truck wheel & some car wheels in the garage ready to be cut up for their alloy, which should help next time!
stinkwheel wrote: |
If you are going to be doing a lot of your own alloy recycling, I'd imagine casting some handy size billets pre-emptively as a job lot then leaving them sitting about the place to age would be a useful thing to do. |
Yep, I'm planning to do this soon once I've cut up some of the scrap.
Freddyfruitbat wrote: | Well impressive and I admire your tenacity!
But having just come across this saga for the first time, and having read the thread from the top, I think personally by now I'd be thinking 'do I really want a milling machine?' |
Thanks! Hahaha I do, and this has all been great fun so I can't complain! ____________________ 2011 XT660Z Ténéré - 2003 YZR-R1 5PW (In Build) |
|
Back to top |
|
You must be logged in to rate posts |
|
 |
|
This page may contain affiliate links, which means we may earn a small commission if a visitor clicks through and makes a purchase. By clicking on an affiliate link, you accept that third-party cookies will be set.

|
You cannot post new topics in this forum You cannot reply to topics in this forum You cannot edit your posts in this forum You cannot delete your posts in this forum You cannot vote in polls in this forum You cannot attach files in this forum You cannot download files in this forum
|
Read the Terms of Use! - Powered by phpBB © phpBB Group
Debug Mode: ON - Server: birks (www) - Page Generation Time: 0.13 Sec - Server Load: 0.51 - MySQL Queries: 17 - Page Size: 152.21 Kb
|