 |
|
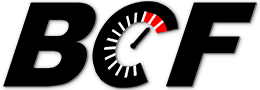 |

|
Author |
Message |
Suntan Sid |
This post is not being displayed .
|
 Suntan Sid World Chat Champion
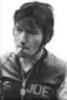
Joined: 07 May 2009 Karma :    
|
 Posted: 16:29 - 15 Dec 2015 Post subject: Engine Building For A Dummy, (Me)! |
 |
|
I'm rebuilding an engine, more for something to do, than anything else.
The engine in question is a Honda Xl125, sohc, circa 1982/3/4.
I know there are plenty of people who can do this with their eyes closed, but I'm sure there are people who are daunted by the prospect. Hopefully this will show these people that it's not as hard as it sounds.
I've done this once before, on a 4 stroke, so I'm a relative noob to it.
I'll try and document as much as I can, including any fcuk ups I make, so you don't have to.
Feel free to chip in, if you think I'm doing anything wrong or you've got any tips or tricks.
This engine will be a combination of two engines I've accquired over the last couple of years, one came as an extra with my project bike and I got the other for £40 from a BCF'er.
The main reason for buying the second engine was that the L/H crankcase on the one I had, had a big chunk missing, just to the rear of the stator housing.
A point worth noting, if you are rebuilding an engine because one of the crankcases is damaged, it's highly unlikely that you could match cases from different engines. As an experiment, I joined two odd cases together, there was a 2mm mismatch on the surfaces where the base gasket would go!
Out of the two engines, one cylinder head was scrap, the cam bearing surfaces were badly scored and the hole for the rear locating pin on the cam bearing was elongated, there was a good chunk of cooling fins missing as well.
The other cylinder head I have is not brilliant, the cam bearing surfaces are good, but it does have a few nicks in the combustion chamber, it should be ok though, I hope.
Of the two camshafts I had, one was badly scored, the other has dicolouration on the tips of the lobes as well as an elongated locating hole for the adv/ret mechanism. I've managed to get a NOS camshaft for £30!
I've got three cylinder barrels, all of which could be rebored. According to the pistons the biggest overbore is 1.5mm, more on this later.
One of the clutch baskets is dead, a lug has snapped off!
I've checked all the clutch plates and springs and they're all well within tolerance, both clutch lifters are very worn.
I've yet to test the stator windings but they look a lot better than the stator I had rewound previously.
I've amassed, nearly, all the new parts I'll need to do the rebuild, these include all bearings, (bar the mains), a full set of oil seals, full gasket set, locknuts for the clutch and oil pump, mounting screws and "O" rings for the oil pump, clutch lifter, new valves and a couple of other nuts and bolts.
https://i645.photobucket.com/albums/uu172/Troodos-Pool-Guy/Eng%20Rbld/New%20bits_zpsetokhjk5.jpg
Initially, I needed to solve a problem I had with the clucth cover, this contains the tacho drive, I had 2 of these, unfortunately, both had the same problem. The tacho cable pushes into a hole, in this cover, where it engages with the worm drive, the cable end is held in place with a bolt, that screws into the housing, across the cable end. On one cover this housing was snapped off completely, on the other the housing was intact but the cable end was stuck in and the cross bolt was snapped.
Someone, (not me), had tried to drill the remains of the bolt out, but the drill had wandered and missed most of the bolt!
Eventually, after many hours, and many sacrificial dremel bits, I managed to get enough space to get a rat tail file in there. A few more hours along the line and I'd managed to file away about 70% of the snapped bolt. Eventually I managed to unscrew the remains of the bolt.
There's not a lot of thread or metal left in the bolt hole now, but it's enough to hold a bolt in, so with some thread lock it should work. I filled in the drill hole with some plastic metal, it's nothing to do with the oil retaining capabilities of the cover so it should be OK.
That was the only problem I had with the crankcases, I got all the locating dowels out, fairly, easily.
I used paint stripper, wet 'n' dry and wire wool to get rid of the layers of old paint, gave it two coats of etch primer and a couple of coats of high temperature enamel, all brushed on.
The reason I've brush painted is I don't have anywhere suitable to spray it, no garage, so I'm doing this in the cellar, and the fumes would get right around the house.
I quote enjoy brush painting so not a big deal really.
I use an artists No.10 brush, so about 1/4 inch of bristles, you can get packs of these for £1, so use a couple of times and bin them. The paint goes on really easily with this brush and doesn't leave any brush marks.
Here are some bits of the engine painted:-
https://i645.photobucket.com/albums/uu172/Troodos-Pool-Guy/Eng%20Rbld/Painted_zpsqtwmakep.jpg
I should say, at this stage, that I have the normal ramge of tools, sockets, spanners, screwdrivers etc. The only specialist tools I have for this are a valve spring compressor, a special castellated socket, an impact driver and a couple of torque wrenches. I keep meing to buy a bench vice but I seem to have got away with G cramps and a set of Mole grips!
First job, of the actual rebuild, is to get the new bearings in!
I managed to get all the old bearings out myself, bar the two blind bearings.
I took the crankcases to my local, old fashioned, bike shop and they got them out for a fiver!
The first three bearings went in with no problems, just driving them in with a mallet, the old bearing and a large socket:-
https://i645.photobucket.com/albums/uu172/Troodos-Pool-Guy/Eng%20Rbld/Bearing%20method%2001_zpsjmt13hnx.jpg
https://i645.photobucket.com/albums/uu172/Troodos-Pool-Guy/Eng%20Rbld/Bearing%20method%2002_zpsccicuqiw.jpg
https://i645.photobucket.com/albums/uu172/Troodos-Pool-Guy/Eng%20Rbld/Bearings%20in_zpsqgjrcgty.jpg
The fourth bearing, for the countershaft, was a different matter, and my first balls up!
I tried to drive it in using the same method as above but it would not go in straight. Unfortunately driving it out again, (a couple of times), is only possible by using the inner race, which has knackered it!
I had another go at getting it in correctly, I did it using this setup:-
https://i645.photobucket.com/albums/uu172/Troodos-Pool-Guy/Eng%20Rbld/Bearing%20method%2003_zpsscu7lm66.jpg
https://i645.photobucket.com/albums/uu172/Troodos-Pool-Guy/Eng%20Rbld/Bearing%20method%2004_zpsffcbokpl.jpg
https://i645.photobucket.com/albums/uu172/Troodos-Pool-Guy/Eng%20Rbld/Bearing%20method%2005_zpslfmoa3g4.jpg
Now it's in it sounds 'orrible!
Fortunately, a new bearing is under a fiver so I've ordered another, next time I'll use the nut, bolt and giant washer set up from the start!
Well that's that's for now, as soon as the new bearing arrives I'll crack on with the gearbox.
This is the, repaired, clutch cover:-
https://i645.photobucket.com/albums/uu172/Troodos-Pool-Guy/Eng%20Rbld/001%20cover%20and%20parts_zpszxaeauyq.jpg
Unfortunately on this cover the clutch actuating arm was worn, there was a ridge forming on the cut out that pushes on the the clutch lifter.
This is easy to get out, there is a small pin that holds the spring on the shaft, it eventually comes out with a set of moleys.
Replacing it is easy, pop in the new oil seal, lube all the mating surfaces, replace the shaft and spring, then knock in the retaing pin. The manual says push the pin into place, in reallity you need to knock it in, carefully, with a toffee hammer!
https://i645.photobucket.com/albums/uu172/Troodos-Pool-Guy/Eng%20Rbld/002%20clutch%20in_zps6ee034md.jpg
The tacho worm drive needed to be replaced, one of the tines on the end had snapped off. It was an absolute bastid to get out, there is a thrust washer and an oil seal holding it in place, years of crud made the oil seal very difficult to get out.
https://images.cmsnl.com/img/partslists/honda-xl125-1978-usa-right-crankcase-cover_mediumhu0040e2205_5774.jpg
I eventually got it out by stabbing it with an awl.
There's plenty of advice on the web about getting this seal out, usually including needle nose pliers. This may well work with a, relatively new, plaible seal but with an old age hardened seal it, simply, won't come out without partially destroying it. Once I'd got it moving, in the housing, the only way of getting the whole shaft out was to prise it out from the bottom with a drift.
Getting the new shaft in is easy, lube everything up, with some engine oil, mount the thrust washer and oil seal on the shaft and push it into place.
To seat the washer and oil seal properly I tapped it in place with an 8mm socket and small hammer!
https://i645.photobucket.com/albums/uu172/Troodos-Pool-Guy/Eng%20Rbld/003%20tacho%20in_zps22jena9k.jpg
https://i645.photobucket.com/albums/uu172/Troodos-Pool-Guy/Eng%20Rbld/004%20tacho%20in_zpsprpgmiva.jpg
https://i645.photobucket.com/albums/uu172/Troodos-Pool-Guy/Eng%20Rbld/005%20tacho%20in_zps5o9lcv1h.jpg
That's it for this casing, the kickstart oil seal and a dowel pin will go on later.
I've got new valves for the cylinder head, had to really as all the valves I had left are bent, therefore they will have to be lapped in.
First thing I need to do is check that the valves seats properly, there is a diagram similar to this in the manual:-
https://www.team-integra.net/images/BAEC1978-D3A7-4405-AB2D-2761DC15A96D/articles/tuan/anglevalves04.jpg
In this case the manual says the seat should be between 1.1 & 1.33m wide. It doesn't say eactly where within the "seat", it should be but I'm assuming anywhere between the lines.
It's quite tricky to measure this but here's how I did it, it only takes a couple of minutes.
I smeared a light coat of engineers blue onto the valve seats in the cylinder head, using a cloth, (you can use a marker pen apparently).
I dropped the valve into the head, holding the valve in place with my thumb, I then turned the valve through 90 degrees backwards and forwards a couple of times.
(DO NOT TURN THE VALVE MORE THAN 90 DEGREES, doing so will give a false reading, it will merely even out over the full 360 degrees)!
There's no point in photographing this, it's way too small.
Once the valve is out of the head you should see a line of "blue" around the valve seat, (on the valve).
https://i645.photobucket.com/albums/uu172/Troodos-Pool-Guy/Eng%20Rbld/0024%20V%20grind_zps4yk6wfcr.jpg
On the exhaust valve there was a strong, complete, blue line around the valve, it's very difficult to measure the thickness of the line, but it's within the limits, AFAICS, which suggests the seal on the valve is good!
The inlet valve has a reasonable blue line around it but there is a section that is not so distinct, which suggests the seal won't be so good.
The valves are new so there is no problem with pitting.
The valve seats are not pitted, but the inlet valve needs a small amount of grinding to get a good all round seal.
I've ground both of them with fine grit:
One, to polish the exhust seat.
Two, to even up the inlet seat.
The whole process took no more than a few minutes.
Here's how I did it:-
Grind the valve, clean off all the grinding paste from the valve and seat, reapply the engineers blue, then check the seating line on the valve, repeat until satified with the results.
The only major problem I had with this was with the grinding stick, 125cc motorcycle valves are small, the exhaust, in particular, actually getting the exhaust valve to adhere to the grinding stick is not easy. In the end I glued it in place with some contact adhesive!
Finally, once satisfied with the results, clean everything to get rid of any trace of grinding paste!
Before I reassemble the valves and springs in the head I need to check the valve guides to make sure they are not worn.
Unfortunately I do not have a dial gauge to measure the lateral movement and the calipers I have won't really do the job, not enough room to get then in!
The ID service limit, of the valve guide is 5.5mm.
I went through my collection of drill bits.
My 5.5mm drill turned out to be 5.31mm diameter! Doh!
I finally found a, random, cheapy, drill bit that had a shank diameter of 5.487mm, this does not fit into the valve guide, therefore it is within the service limit.
I've checked the inner and outer valve springs and they're all, well, within the service limits so I can go ahead and get the valves in.
To get the valves and springs fitted into the head, you'll need a valve spring compressor, a blob of grease and some oil to lubricate everything as you assemble the valves. It's handy to have a magnet on a stick, you will drop the collets at some point and this makes it very easy to extract them!
https://i645.photobucket.com/albums/uu172/Troodos-Pool-Guy/Eng%20Rbld/0025%20Spring_zpsddkm6jql.jpg
One thing you need to remember is, valve springs are progressive springs, the coils are further apart as you get higher up the spring. The coils that are closer together need to be facing down, ie nearest to the cylinder head!
Right, these little boogers, the valve collets, can be a right PITA to fit on the valve stems:-
https://www.xs650direct.com/parts/img250/01-9093.jpg
What you need to be thinking about, when you compress the valve spring, is where the groove, in the valve, is in relation to the retaining washer/cap surface, on top of the spring.
When you've compressed the spring you want the groove in the valve stem to be about 2 to 3mm below the washer/cap, the collets should then drop in to place, realtively, easily.
If you've got this distance right, when you press the collets down, (no great pressure required), you will hear a tiny click as the locking rim engages into the groove on the valve stem.
All you need to do then is slacken the compressor off, slowly, and the collets will be in place!
One other thing to note, you do have to take liberties with the valve spring compressor.
When compressed the valve stem will not be central in the valve spring cap, you need to wrestle it to and fro and hold it in place so everything is centred up!
https://i645.photobucket.com/albums/uu172/Troodos-Pool-Guy/Eng%20Rbld/0026%20Spring_zpsg0zo1bk6.jpg
https://i645.photobucket.com/albums/uu172/Troodos-Pool-Guy/Eng%20Rbld/0027%20Spring_zpse9e6tfgm.jpg
I got the valve collets in very easily, using the method I described, took no more than 10 mins to do the whole head.
In other news, I got the replacement bearing I needed this morning, that went in really easily. My new camshaft also arrived this morning but obviously the postman CBA, actually, delivering it or ringing the doorbell and left the usual card, ,which means I can't get my hands on it until tomorrow!
That's it for now, more to follow.
TLDR? Meh, you're a goldfish! ____________________ "Everybody needs money, that's why they call it money!"  |
|
Back to top |
|
You must be logged in to rate posts |
|
 |
Pete. |
This post is not being displayed .
|
 Pete. Super Spammer

Joined: 22 Aug 2006 Karma :     
|
 Posted: 18:07 - 15 Dec 2015 Post subject: |
 |
|
How did you clean the top face of the cylinder head Sid? Looks like you used emery or something similar. ____________________ a.k.a 'Geri'
132.9mph off and walked away. Gear is good, gear is good, gear is very very good  |
|
Back to top |
|
You must be logged in to rate posts |
|
 |
Suntan Sid |
This post is not being displayed .
|
 Suntan Sid World Chat Champion
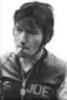
Joined: 07 May 2009 Karma :    
|
 Posted: 18:37 - 15 Dec 2015 Post subject: |
 |
|
Pete. wrote: | How did you clean the top face of the cylinder head Sid? Looks like you used emery or something similar. |
Not with anything remotely resembling emery.
I used a green plastic kitchen scourer, or "Scotchbrite" if you like.
If you squirt a bit of WD40 or meths on it, it's not too hard to get it clean, just requires a bit of elbow grease!
I've just had alook at it, it looks worse than it is in reality, there's a layer of oil on it, at the moment!
That head was already off the engine when I got it, it looks like it's been on and off a few times. There were the reamains of a paper gasket and instant gasket, it's not in brilliant condition, but I've checked with a straight edge and, AFAICS, it's flat! ____________________ "Everybody needs money, that's why they call it money!"  |
|
Back to top |
|
You must be logged in to rate posts |
|
 |
stevo as b4 |
This post is not being displayed .
|
 stevo as b4 World Chat Champion
Joined: 17 Jul 2003 Karma :   
|
|
Back to top |
|
You must be logged in to rate posts |
|
 |
Suntan Sid |
This post is not being displayed .
|
 Suntan Sid World Chat Champion
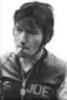
Joined: 07 May 2009 Karma :    
|
|
Back to top |
|
You must be logged in to rate posts |
|
 |
Suntan Sid |
This post is not being displayed .
|
 Suntan Sid World Chat Champion
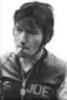
Joined: 07 May 2009 Karma :    
|
|
Back to top |
|
You must be logged in to rate posts |
|
 |
Pete. |
This post is not being displayed .
|
 Pete. Super Spammer

Joined: 22 Aug 2006 Karma :     
|
|
Back to top |
|
You must be logged in to rate posts |
|
 |
Suntan Sid |
This post is not being displayed .
|
 Suntan Sid World Chat Champion
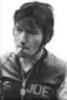
Joined: 07 May 2009 Karma :    
|
 Posted: 14:40 - 16 Dec 2015 Post subject: |
 |
|
Next on the agenda is getting the gearbox, Kickstart mechanism and crank assembled into the crankcases.
Before doing this I need to check everything is in a good usable condition.
According to the "Haynes" the first thing that needs to go in is the kickstart mechanism.
I've got two to choose from, I'll be picking the best parts from both to, hopefully, make one good one.
https://i645.photobucket.com/albums/uu172/Troodos-Pool-Guy/Eng%20Rbld/001%20Kick_zpsacqdyyug.jpg
At first glance they seem to be in, roughly, the same condition.
However a closer inspection reveals that the teeth on one of the starter pinnions are quite badly damaged, so that will be heading for the scrap heap.
https://i645.photobucket.com/albums/uu172/Troodos-Pool-Guy/Eng%20Rbld/002%20Kick_zpsfyqblb94.jpg
Now they're apart a few things show up, the lower of the two, in the photo, is in the worst condition, as well as the pinnion teeth having bits missing, the spring on the rachet mechanism seems to have lost some of its "spring", it's shorter than the other one.
Also the return spring is showing signs of wear, there is a kink forming where it locates into the shaft.
I'll be using the top one in the photo.
According to the manual the tolerances that need to be checked are the ID of the pinnion wheel and the OD of the shaft where the pinnion runs.
The shaft is not worn at all, the pinnion is slightly out but well within the tolerance allowed.
The only thing I have to be careful about when reassembling this is lining up some punch marks, one on the ratchet and the other on the shaft. These punch marks are very small and also quite difficult to line up, basically, because they're not on the same plane, (Old farts like me may need a magnifying glass).
Funnily enough I can't find any punch marks on the one I'm not using, maybe it's not a genuine Honda part.
Other than that It's easy to put it back together, all I need is a pair of circlip pliers and some oil to lube everything up.
https://i645.photobucket.com/albums/uu172/Troodos-Pool-Guy/Eng%20Rbld/003%20Kick_zpsc40roijf.jpg
All done easy, peasy!
Picked up my mew camshaft this morning, here it is:-
https://i645.photobucket.com/albums/uu172/Troodos-Pool-Guy/Eng%20Rbld/004%20Cam_zps3unldtfh.jpg
A bit of googling reveals that a new camshaft will/should come with one or two coatings on it, a rust inhibiting grease and a phosphate covering.
There's no grease on this one, it's dry to touch, if there was I would have to remove this. The phosphate coating is there to help with bedding in all the mating surfaces.
When installing the camshaft I must coat all the mating surfaces, including the lobes, with molybdenum disulphide grease.
That's all for now, I'll be having a look at the gears and selector mechanism next! ____________________ "Everybody needs money, that's why they call it money!"  |
|
Back to top |
|
You must be logged in to rate posts |
|
 |
Suntan Sid |
This post is not being displayed .
|
 Suntan Sid World Chat Champion
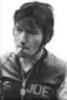
Joined: 07 May 2009 Karma :    
|
 Posted: 14:33 - 17 Dec 2015 Post subject: |
 |
|
Gearbox.
A quick visual inspection reveals that on the parts here:-
https://i645.photobucket.com/albums/uu172/Troodos-Pool-Guy/Eng%20Rbld/007%20join_zpsx1evjujl.jpg
the starter pinnion has a chipped tooth, so that's no good, no doubt related to the knackered teeth on the kickstart pinnion.
There doesn't appear to be any damage to any other teeth, on either cluster. A visual check on the splines for the drive sprocket shows that the shaft in the photo is good, the other one I have is not so I'll go with the two in the photo.
The tolerances that need to be checked within the gearbox are confined to the selctor forks, shaft and drum, according to "Haynes". The only thing it mentions for the gear clusters is a visual inspection, which I've done, and to check that everything is in the right order on the shafts.
To be frank, I forgot to buy new circlips for the gearbox so I'm not going to strip everything off the shafts. I took off as much as I could without removing any circlips, I appear to have all the parts, everything appears to be in the right place and the right order.
Here's the selector drum and forks:-
https://i645.photobucket.com/albums/uu172/Troodos-Pool-Guy/Eng%20Rbld/008%20join_zpszsktgvwr.jpg
I need to measure the OD selector shaft, the ID of the selector forks, and the thickness at the end of the fork arms.
The shaft OD is not good but it's still within the tolerance allowed.
The ID of the selector forks is very good.
The fork arms don't seem to have worn at all.
Before dimantling the selector forks take a note of what order they are in, on the shaft, as far as I can see there are no markings on then to suggest where they fit or what way up they're supposed to go! Maybe I'm missing something
As far as the crankshaft goes, the main bearings seem good, they run quietly and smoothly, I think they have been replaced before.
The axial clearance at the big end is way under the service limit at 0.3mm, the service limit is 0.8mm. I can't detect any vertical movement on the con rod and it runs smoothly.
As this is a pressed crank, I'm not going to delve any further and, rightly or wrongly, I'm going to assume that it's good to go.
Everything seems to be ready to go, so I can start getting all this stuff into the crankcase.
Now the fun bit, getting the gear cluster and selector mechanism into the crankcase.
The manual tells you to put all the parts together, in a clump, and drop them into the crankcase.
In practice, unless you've got thin, spindly, fingers, this extremely difficult, the clearances for your fingers are tiny. To add to the complications both the mainshaft and the countershaft have thrust washers at the bottom, this wouldn't be to bad but on the mainshaft the washer is splined, so if this falls off there's no chance of the shaft just dropping through it, into place.
I did it like this.
Lube everything, with some engine oil, I'm using 20/50.
Grease the thrust washers on both shafts then align the shafts on the bench.
Carefully lift both shafts together amd lower them, carefully into the bearings.
Once they're in the gears will not turn 360 degrees, don't worry, once you get the selector arms, shaft and drum in everything will line up.
With both shafts in place, take the selector arms, (ensuring they're in the right order and the right way up), and insert them into the slots within the gear clusters.
Move the selector arms out of the way a bit, and insert the selector drum.
Now you need to get the lugs on the selector arm into place on the selector drum, this is a bit fiddly, but after a bit of wiggling they should all go in.
Now you can insert the selector arm shaft through the selector arms and into the housing in the casing. (Don't put too much oil into this housing, it's a blind hole and excess oil does not get squeezed out).
You can see the contact for the neutral switch on the bottom of the selector drum, so I've put the gearbox in neutral. I don't know whether this good practice or not, there's no mention of what to do in the manual.
Gear cluster and selector in:-
https://i645.photobucket.com/albums/uu172/Troodos-Pool-Guy/Eng%20Rbld/001%20Join_zpsrcclusfc.jpg
Crank in:-
https://i645.photobucket.com/albums/uu172/Troodos-Pool-Guy/Eng%20Rbld/002%20join_zpseqt1mqzi.jpg
Kickstart in:-
https://i645.photobucket.com/albums/uu172/Troodos-Pool-Guy/Eng%20Rbld/003%20join_zpsb3fvzxnp.jpg
Gasket on:-
https://i645.photobucket.com/albums/uu172/Troodos-Pool-Guy/Eng%20Rbld/004%20join_zpsisb2rvwp.jpg
Crankcase on:-
https://i645.photobucket.com/albums/uu172/Troodos-Pool-Guy/Eng%20Rbld/005%20join_zpszxm14nvv.jpg
Torqued up:-
https://i645.photobucket.com/albums/uu172/Troodos-Pool-Guy/Eng%20Rbld/006%20join_zpssg2sj8pg.jpg
Now the real story!
Once I'd got everything into the LH crankcase, I could not the RH crankcase to join up. I had everything in and out numerous times but whatever I tried I could not get the crankcases to meet up, there was a 5mm gap between the two.
When I had everything out, I measured, cleaned and reassembled everything, still couldn't get everything to fit.
I started again, adding one part at a time and test fitting the other crankcase. Eventually the problem turned out to be a combination of things, I'd made a mistake with the position of the starter pinnion on the countershaft and both the countershaft and mainshaft hadn't seated fully in the bearings. I resisted the temptation to hit it with a big hammer!
Once I'd sorted that out, it was the kickstart mechanism that was causing a problem.
When the kickstart is mounted, in the RH cover, the return spring pushes the whole thing out of alignment. The shaft, on the kick start does not run in a bearing, of any sort, in the RH casing, it just protudes through an oversize hole. As well as this the pinnion on the kickstart has to be meshed with it's mate on the countershaft, you can't actually see this so there's a bit of hit and miss about it. So, when you're trying to fit everything together, not only are you trying to drop the crankcase into place, but you have to try and force the kickstart shaft into alignment with that spare hand you've got knocking around!
That's a few hours of my life I won't be getting back, but it's all in place now. Probably going to take a bit of break now and see what santa brings!
More to follow, eventually. ____________________ "Everybody needs money, that's why they call it money!"  |
|
Back to top |
|
You must be logged in to rate posts |
|
 |
RhynoCZ |
This post is not being displayed .
|
 RhynoCZ Super Spammer

Joined: 09 Mar 2012 Karma :     
|
 Posted: 16:58 - 17 Dec 2015 Post subject: |
 |
|
Great thread Sid, I've read it during my lunch and got hooked, can't wait to see it complete.  ____________________ '87 Honda XBR 500, '96 Kawasaki ZX7R P1, '90 Honda CB-1, '88 Kawasaki GPz550, MZ 150 ETZ
'95 Mercedes-Benz w202 C200 CGI, '98 Mercedes-Benz w210 E200 Kompressor |
|
Back to top |
|
You must be logged in to rate posts |
|
 |
Suntan Sid |
This post is not being displayed .
|
 Suntan Sid World Chat Champion
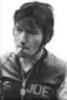
Joined: 07 May 2009 Karma :    
|
 Posted: 17:21 - 17 Dec 2015 Post subject: |
 |
|
There'll be more soon, I've been doing a bit more this afternoon.
I've not decided what I'm going to do about the barrel and piston yet!
Whatever I do there'll be a break in proceedings when I get to the stage when the piston and barrel can go on! ____________________ "Everybody needs money, that's why they call it money!"  |
|
Back to top |
|
You must be logged in to rate posts |
|
 |
Suntan Sid |
This post is not being displayed .
|
 Suntan Sid World Chat Champion
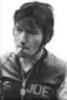
Joined: 07 May 2009 Karma :    
|
 Posted: 21:52 - 17 Dec 2015 Post subject: |
 |
|
Time to get the, gear selector, shifter, clutch, oil pump and oil filter in.
https://i645.photobucket.com/albums/uu172/Troodos-Pool-Guy/Eng%20Rbld/001A%20gear%20selector_zpsmxfknkxr.jpg
This lot bolts onto the crankcase and the top of the selector drum, it's a bit fiddly getting the spring in place, but easy really.
https://i645.photobucket.com/albums/uu172/Troodos-Pool-Guy/Eng%20Rbld/001A%20shift%20arm_zps947nqwiv.jpg
The gear shift mechanism is just pushed through the case, all you have to look out for is that the ends of the spring make proper contact with the star shaped wheel. In my box of bits I had four of these things, the one I put in was the only one that wasn't worn.
https://i645.photobucket.com/albums/uu172/Troodos-Pool-Guy/Eng%20Rbld/001A%20clutch_zpsq22wxqrf.jpg
Here's the clutch, yay, new parts, new bearing, new lock nut and new clutch lifter.
This all goes on, relatively, easily,
The springs were well within tolerance.
https://i645.photobucket.com/albums/uu172/Troodos-Pool-Guy/Eng%20Rbld/001A%20oil%20pump_zpsbo0a4dia.jpg
The clearances on the oil pump are good, so that's an easy bolt on, new gasket and new screws on the oil filter cover, (they're alway chewed).
https://i645.photobucket.com/albums/uu172/Troodos-Pool-Guy/Eng%20Rbld/001A%20comp_zpsu0gebb6i.jpg
And that's everything in, for now.
The only thing I can't do, at the moment, is tighten up the, new, lock nuts on the oil pump and clutch, they both have a torque setting of 47Nm.
I simply can't do that on the bench, even with the engine in the frame, someone sitting on it, the bike in gear and the back break on, it's hard enough. I'll have to wait until the engine's in the frame, it's on my "to do" list! ____________________ "Everybody needs money, that's why they call it money!"  |
|
Back to top |
|
You must be logged in to rate posts |
|
 |
Suntan Sid |
This post is not being displayed .
|
 Suntan Sid World Chat Champion
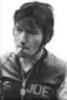
Joined: 07 May 2009 Karma :    
|
 Posted: 15:25 - 19 Dec 2015 Post subject: |
 |
|
Contrary to what I said in the previous post, I have managed to tighten the lock nuts on both the clutch and oil pump.
The oil pump is easy, two small strips of wood across the cylinder hole in the crankcase, an old gudgeon pin in the con rod, locking the crank, and the nut is tightened easily!
The clutch is another matter, it looks like I was well and truly "Haynesed"!
In the manual it says, I'm paraphrasing:-
Quote: | fit the clutch assembly, including the friction plates, now fit the washer and lock nut and tighten to 36ft lb |
There's even a picture of this in the manual, FFS!
The problem with doing it as decribed is that there is no pressure on the friction plates, even if you lock up the primary drive and lock the crank, (as above), beacuse the clutch is slipping the countershaft still rotates.
IMO, there is no way of locking the countershaft without damaging the spline, for the sprocket.
What the "Haynes" should have said is:-
Quote: | fit the clutch assembly, including the friction plates, fit the washer and lock nut, fit the clutch springs and torque to the correct value, now tighten the lock nut to 36ft lb |
With the clutch springs fitted, (and no consequent clutch slip), the gears engaged and the crank locked, (as described), I had no problem torqueing up to 36ft lb.
The clutch cover and new gasket is now on!
More soon! ____________________ "Everybody needs money, that's why they call it money!"  |
|
Back to top |
|
You must be logged in to rate posts |
|
 |
Shaft |
This post is not being displayed .
|
 Shaft World Chat Champion

Joined: 27 Dec 2010 Karma :    
|
 Posted: 01:21 - 20 Dec 2015 Post subject: |
 |
|
Next time you have a go at hammering in bearings, make your life a bit easier by putting the case in the oven and the bearings in the freezer.
No need to go mental, an hour or so on a low heat, same for the freezer, you might find they drop right in. ____________________ Things get better with age; I'm close to being magnificent........
20 RE Interceptor, 83 Z1100A3, 83 GS650 Katana
WooHoo, I'm a Man Point Millionaire! https://www.bikechatforums.com/viewtopic.php?t=234035 |
|
Back to top |
|
You must be logged in to rate posts |
|
 |
Suntan Sid |
This post is not being displayed .
|
 Suntan Sid World Chat Champion
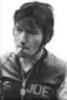
Joined: 07 May 2009 Karma :    
|
 Posted: 02:00 - 20 Dec 2015 Post subject: |
 |
|
Shaft wrote: | Next time you have a go at hammering in bearings, make your life a bit easier by putting the case in the oven and the bearings in the freezer.
No need to go mental, an hour or so on a low heat, same for the freezer, you might find they drop right in. |
That's what I did!
The casing was sitting on top of the rayburn, (not on the hotplate), over night and the bearings were in the freezer over night.
All the other bearings went in easily, that particular one didn't.
When I got the replacement, a different make, that went in easily, I got it in halfway with just finger pressure!
Draw your own conclusions! ____________________ "Everybody needs money, that's why they call it money!"  |
|
Back to top |
|
You must be logged in to rate posts |
|
 |
Shaft |
This post is not being displayed .
|
 Shaft World Chat Champion

Joined: 27 Dec 2010 Karma :    
|
 Posted: 02:16 - 20 Dec 2015 Post subject: |
 |
|
Suntan Sid wrote: | Shaft wrote: | Next time you have a go at hammering in bearings, make your life a bit easier by putting the case in the oven and the bearings in the freezer.
No need to go mental, an hour or so on a low heat, same for the freezer, you might find they drop right in. |
That's what I did!
The casing was sitting on top of the rayburn, (not on the hotplate), over night and the bearings were in the freezer over night.
All the other bearings went in easily, that particular one didn't.
When I got the replacement, a different make, that went in easily, I got it in halfway with just finger pressure!
Draw your own conclusions! |
I'd like to say that's the problem with non original parts, but there's no pattern (see what I did there ) to it.
Not even all OE parts fit right first time. ____________________ Things get better with age; I'm close to being magnificent........
20 RE Interceptor, 83 Z1100A3, 83 GS650 Katana
WooHoo, I'm a Man Point Millionaire! https://www.bikechatforums.com/viewtopic.php?t=234035 |
|
Back to top |
|
You must be logged in to rate posts |
|
 |
Suntan Sid |
This post is not being displayed .
|
 Suntan Sid World Chat Champion
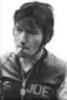
Joined: 07 May 2009 Karma :    
|
 Posted: 15:44 - 22 Dec 2015 Post subject: |
 |
|
Going Large!
Well, santa has delivered, early!
Of course, I have committed the cardinal sin of BCF, , and bought a big bore kit, however, I will not be standing on the naughty step, a full license says I can do what the #%*k I want, so there!
This is a big bore kit for a Honda TL125 trials.
As it stands, after a few calculations, it will take my 125 to 144cc.
If I want to leave a minimum of 2mm thickness on the liner skirt I can go to a maximum 158cc.
According to a big yellow book, at my friendly motorcycle shop, the original XL125 barrel can be overbored by 2.5mm, this would leave a liner skirt thickness of a mere 1mm. I'm not sure whether this is a good idea or not.
I won't do it, however it would equate to an absolute maximum of 164cc.
This kit will work on any XL125, however pre 1982 models have a smaller opening in the crankcase for the cylinder liner so this would have to be machined to accept the new barrel, it's a straight fit on mine.
No doubt someone will be itching to tell me I should have gone down the XL185 path.
I could, but to do a complete engine swap would require finding a, rare as rocking horse poo, 185 engine, (actually 180cc).
Being as rare as the proverbial, even a shonky, barn/pond find motor is a minimum £300 and that's before the complete strip and rebuild.
The 185 crank has smaller mains, a longer stroke and the barrel is a different height, so it's not just a case of swapping a few parts.
As you can see the new barrel has much more in the way of cooling fins.
The piston has been machined to accomodate the cylinder head, I've also got modified base and head gaskets.
https://i645.photobucket.com/albums/uu172/Troodos-Pool-Guy/Eng%20Rbld/001%20Bigbore_zpsyrpwcqun.jpg
Time to wrestle in some piston rings.
More soon! ____________________ "Everybody needs money, that's why they call it money!"  |
|
Back to top |
|
You must be logged in to rate posts |
|
 |
Pete. |
This post is not being displayed .
|
 Pete. Super Spammer

Joined: 22 Aug 2006 Karma :     
|
 Posted: 15:54 - 22 Dec 2015 Post subject: |
 |
|
Size the rings before you fit them and check the end gap. Pop a ring into the bottom of the cylinder then gently push it up to the top using the piston skirt to make sure it's sitting square. Measure end gap then repeat for other ring. ____________________ a.k.a 'Geri'
132.9mph off and walked away. Gear is good, gear is good, gear is very very good  |
|
Back to top |
|
You must be logged in to rate posts |
|
 |
Suntan Sid |
This post is not being displayed .
|
 Suntan Sid World Chat Champion
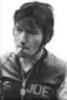
Joined: 07 May 2009 Karma :    
|
|
Back to top |
|
You must be logged in to rate posts |
|
 |
Suntan Sid |
This post is not being displayed .
|
 Suntan Sid World Chat Champion
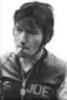
Joined: 07 May 2009 Karma :    
|
 Posted: 16:33 - 22 Dec 2015 Post subject: |
 |
|
According to the manual the ring gaps should be between 0.15 and 0.35 mm with a service limit of 0.5mm.
The new rings came in at 0.20mm! ____________________ "Everybody needs money, that's why they call it money!"  |
|
Back to top |
|
You must be logged in to rate posts |
|
 |
Suntan Sid |
This post is not being displayed .
|
 Suntan Sid World Chat Champion
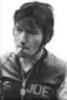
Joined: 07 May 2009 Karma :    
|
 Posted: 16:46 - 22 Dec 2015 Post subject: |
 |
|
I'm using this as a guide to installing the rings:-
Clicky
Tells you what you need to know, although I think they've lifted the pictures from Haynes! ____________________ "Everybody needs money, that's why they call it money!"  |
|
Back to top |
|
You must be logged in to rate posts |
|
 |
Pete. |
This post is not being displayed .
|
 Pete. Super Spammer

Joined: 22 Aug 2006 Karma :     
|
|
Back to top |
|
You must be logged in to rate posts |
|
 |
Suntan Sid |
This post is not being displayed .
|
 Suntan Sid World Chat Champion
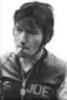
Joined: 07 May 2009 Karma :    
|
 Posted: 19:09 - 22 Dec 2015 Post subject: |
 |
|
OK, a little more progress!
Rings on, piston connected to con rod, base gasket on, locating dowels in and barrel now in place:-
https://i645.photobucket.com/albums/uu172/Troodos-Pool-Guy/Eng%20Rbld/003%20Bigbore_zpsqzi7bruq.jpg
https://i645.photobucket.com/albums/uu172/Troodos-Pool-Guy/Eng%20Rbld/002%20Bigbore_zpsbzgqkmze.jpg
It's a bit fiddly indexing the piston ring ends and getting the barrel over the piston.
A light coating of oil in the barrel.
Stop the piston moving with a couple of pieces of wood on the crankcases.
Slide the barrel over the studs, then carfully compress each ring with your finger nails and pull the barrel down with any extra fingers or thumbs you have knocking round.
As I said its a bit fiddly, you don't need any real force to do it, whatever you do don't resort to hitting anything with a persuader.
Keep an eye on the rings as your doing it and you'll see what's stopping it all sliding together easily.
A few turns on the crank reveals everything is working as it should be!
Well that really is it for a while, I need to order a new cam chain, it's not worth skimping, considering the other new parts I've used.
I've got two knocking around but I don't know how old they are and one of them seems to have a soft link.
Once that arrives I can get on with the head, valve, timing, flywheel and ignition. ____________________ "Everybody needs money, that's why they call it money!"  |
|
Back to top |
|
You must be logged in to rate posts |
|
 |
Suntan Sid |
This post is not being displayed .
|
 Suntan Sid World Chat Champion
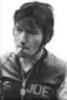
Joined: 07 May 2009 Karma :    
|
 Posted: 21:58 - 24 Dec 2015 Post subject: |
 |
|
Cam chain and camshaft.
Unbelievably, considering the time of year, my new cam chain arrived this morning, free postage and it arrived in less than 48hrs!
So to work, here are the components of the cam chain tensioner:-
https://i645.photobucket.com/albums/uu172/Troodos-Pool-Guy/Eng%20Rbld/01%20A%20tensioner_zpsfgvtlwmo.jpg
The more observant of you may have noticed a piece of spoke.
There's a neat little trick you can do with this, on this particular tensioner mechanism.
The shaft on the tensioner has a tapped 3mm hole bored into it, I've put a 3mm thread on the piece of spoke, this allows you to tighten or loosen the cam chain tension easily. rather than poking at it and damaging it with an old screwdriver. I had to retap the hole in the shaft, PO's have been poking at it with the wrong implement!
This is how I'm locking the crank, to allow me to tighten the flywheel onto the crank:-
https://i645.photobucket.com/albums/uu172/Troodos-Pool-Guy/Eng%20Rbld/02%20A%20lock_zps2tlr4tge.jpg
Here's the tensioner and cam chain fitted, waiting for the flywheel to go on:-
https://i645.photobucket.com/albums/uu172/Troodos-Pool-Guy/Eng%20Rbld/03%20A%20chain%20on_zpsn4u0b9qd.jpg
The flywheel, now torqued on:-
https://i645.photobucket.com/albums/uu172/Troodos-Pool-Guy/Eng%20Rbld/04%20A%20flywheel_zpse5zprlxq.jpg
Barrel, gaskets and tensioner arms in place:-
https://i645.photobucket.com/albums/uu172/Troodos-Pool-Guy/Eng%20Rbld/05%20A%20barrel_zpsdve5ksl1.jpg
Cylinder head in place, this is a bit of a faff, you could really do with an extra set of hands:-
https://i645.photobucket.com/albums/uu172/Troodos-Pool-Guy/Eng%20Rbld/06%20A%20head_zpsdfjgtfnh.jpg
I have to put the rocker cover on next and torque up the cylinder head before I can fit the camshaft and cam chain:-
https://i645.photobucket.com/albums/uu172/Troodos-Pool-Guy/Eng%20Rbld/07%20A%20cam%20rocker_zpsb29eb7tj.jpg
All torqued up:-
https://i645.photobucket.com/albums/uu172/Troodos-Pool-Guy/Eng%20Rbld/08%20A%20rocker%20on_zps9m4sr062.jpg
Cam and camchain in and timed:-
https://i645.photobucket.com/albums/uu172/Troodos-Pool-Guy/Eng%20Rbld/09%20A%20done_zpsytq64aqq.jpg
If you've not done this before, it's quite an awkward thing to do.
On this, small, engine there's not a lot of room to get your fingers in, to manouvre the cam sproket and chain into place. This is further complicated by having to keep the cam and crank aligned with the timing marks and keeping enough tension on the cam chain, to stop it dropping off the crank sprocket.
This is what really happened!
Everything was going fine until it came to fitting my new camshaft.
As per the instructions in the manual, I torqued the head down.
I tied to insert the camshaft but it simply would fit, I could get it in to the point where the journals started to mate with the bearing surfaces, but that was as far as it would go.
After a lot messing around, trying to get the bloody thing in, I, inevitably, dropped the cam chain, this forced me to start again!
I manged to get the chain back on the crank sprocket once I'd removed the head and rocker cover.
With the new cam seemingly not fitting I started again, this time I didn't torque down the head and the cam slipped into place easily, however, tightening the head nuts to just finger tight completely stopped the cam rotating!
This didn't feel right, so I removed the head and rocker cover again.
Starting again, this time I used my old camshaft, torqued the head down and the old camshaft fitted easily, and rotated easily!
So that's where I'm at.
What I should have done is measure the camshaft journals on the old camshaft before I installed it and compared that to the journals on the new camshaft. I have measured the journals on the new cam and they appear to be 0.05mm larger than specifications.
The new cam does have a coating on it, the journals also feel quite rough in comparison to the old cam. From what I've read on the web I should not remove this coating as it, apparently, aids the bedding in process.
Should I polish this coating off to get the cam to fit?
As I said in the opening post, the old cam is a slightly worse for wear and I'd prefer to use the new one if possible?
Any thoughts? ____________________ "Everybody needs money, that's why they call it money!"  |
|
Back to top |
|
You must be logged in to rate posts |
|
 |
Pete. |
This post is not being displayed .
|
 Pete. Super Spammer

Joined: 22 Aug 2006 Karma :     
|
 Posted: 00:42 - 25 Dec 2015 Post subject: |
 |
|
I would not leave anything that could be considered abrasive on a journal for assembly. Clean it up and offer it up again.
Saying that 0.05mm is 2 thou which is standard interference fit for stuff like valve seats. If it's that much oversize it's doubtful that it's ever going to turn. ____________________ a.k.a 'Geri'
132.9mph off and walked away. Gear is good, gear is good, gear is very very good  |
|
Back to top |
|
You must be logged in to rate posts |
|
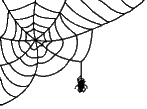 |
Old Thread Alert!
The last post was made 8 years, 125 days ago. Instead of replying here, would creating a new thread be more useful? |
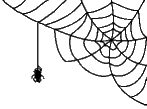 |
|
|
This page may contain affiliate links, which means we may earn a small commission if a visitor clicks through and makes a purchase. By clicking on an affiliate link, you accept that third-party cookies will be set.

|
You cannot post new topics in this forum You cannot reply to topics in this forum You cannot edit your posts in this forum You cannot delete your posts in this forum You cannot vote in polls in this forum You cannot attach files in this forum You cannot download files in this forum
|
Read the Terms of Use! - Powered by phpBB © phpBB Group
Debug Mode: ON - Server: birks (www) - Page Generation Time: 0.12 Sec - Server Load: 0.4 - MySQL Queries: 17 - Page Size: 188.5 Kb
|